Presentation Transcript
AI x Biotech: How We Made Vanillin ex-Ferulic Acid Greener, Cheaper and Faster
This transcript of Orchidlinn Chief Science Officer Dr Wu’s presentation at FI Europe in November 2024 gives us a front row seat into the future of biotech for hard-to-farm ingredients.


Hello. I am Dr Wu.
Today I’m excited to share with you: How we made vanillin ex-ferulic acid greener, cheaper and faster.

I’m a biotech scientist. It’s hard to imagine how incredibly complex our work is.
Synthetic biology involves taking apart biology at the foundational levels, like genes and cell parts, then reassembling them into novel living systems.
We could spend years trying to discover the right strain of microorganisms or enzymes.
Followed by even more years engineering them to behave in a certain way.
We run countless tests and retests to stabilise results and ensure they are always high-performing and repeatable.
Lots of data. Laborious. Detail-oriented work.
Imagine what AI can do for someone like me.
Imagine what AI can do for vanillin.

Natural vanillin, extracted from vanilla beans, is one of many flavour, fragrance, nutraceutical and beauty ingredients that traditional agriculture cannot supply at scale and with consistent quality.
Unstable supply. Unstable quality. Unstable prices.
That’s why natural vanillin from vanilla beans is not used in 99% of vanilla flavoured products.

Instead, over 80% of these products use synthetic or artificial vanillin.
Synthetic vanillin is made by chemically synthesizing guaiacol or lignin.
These chemical processes are energy intensive.
They use hazardous chemicals and produce toxic waste.
It’s a high pollution industry.
Most of the guaiacol comes from petrochemical sources and leaves a leathery aftertaste.
Quality is not good.
But it’s cheap. And supply is stable.

Global consumption of vanillin is expected to more than double by 2033…

… to 76,000 tons. How much of it will be sustainable and natural?

The third type of vanillin in the market is bio-synthesized vanillin.
Bio-synthesized vanillin uses rice husks as the feedstock to produce ferulic acid, which is then fermented using enzymes.
Rice husks is a renewable agricultural waste product.
By transforming it into a high value product, that’s circular economy in action.

Unlike chemically processed vanillin, the bioconversion process is mild.
Low energy use. No hazardous chemicals. No toxic waste.
Using only natural ingredients and natural processes.
It’s natural. It’s sustainable. It can be produced at scale.

So why is it not more widely used?

Experiments in R&D are designed to try and achieve a certain positive rate, or a high percentage of successful mutations.
However, there is no guarantee that any given experiment will be successful.
That’s why the R&D stage involves countless experiments for saturation mutation, directed evolution, random mutation and so on.
This stage normally takes 2 years to complete.

By using machine learning algorithms, AI can analyze massive amounts of experimental data and accurately predict experimental outcomes.
Compared to traditional R&D cycles, the optimization process is much more streamlined, with a clear direction for enhancing hit rates.
Furthermore, the speed of optimization improves exponentially with each new round of experimentation.
AI's ability to process and analyze large datasets helps our R&D team navigate the path-finding and enzyme discovery stages up to 12x faster.
Cutting R&D time to just two months.

Pilot trials are traditionally conducted after the R&D stage is completed.
During the process of converting the R&D results into a production process and establishing the reaction system, the enzyme activity and thermal stability are often relatively low.
This requires repeatedly optimizing the enzyme in order to improve the enzyme activity.
The direction of this optimization process is unpredictable.
The whole process takes up to two years to complete.

With AI, pilot trial experiments can start early.
In fact, they can start at the same time as R&D.
During the establishment of the reaction system, AI can predict and intervene to address issues related to enzyme activity, conversion rate, and thermal stability.
This determines the optimal enzyme engineering direction earlier.
There’s no need for repeated experiments.
In addition, AI can simulate and optimize the production process, leading to improvements in both production efficiency and product quality.
Pilot trials can now be completed in 4 months.

After 90% of the pilot trials are completed, the process then moves to the mid scale trial stage.
This stage involves conducting process verification, strain optimization, and enzyme optimization.
The process is lengthy and has low efficiency.
If any issues arise, it means going back to the R&D or pilot trial stage to conduct more experimental validation.
This usually takes up to a year to complete.

With AI, we can start mid scale trials by the time pilot trials reach 50% completion.
That’s a 40% reduction in the overall development cycle compared to traditional approaches.
All this time, AI is actively engaged in predictive analysis and continuous optimization during the R&D and pilot stages.
The issues related to process development, enzymes, and microbial strains encountered during mid scale trials are greatly reduced.
Not only that, AI rapidly and continuously performs equipment parameter adjustments and optimizations.
We can complete mid scale trials in under 8 months.

The key challenges that need to be addressed during full scale production include a variety of technical issues.
Supply chain management. Production efficiency. Cost control.
Establishing a robust quality system often requires a significant amount of time and effort.
Full scale production typically takes 6-12 months.
From R&D to production, conventional biotech takes a total of 5-6 years.

Currently we are exploring the use of AI in automating fermentation-based production processes.
This approach is expected to further enhance the development cycle and improve overall efficiency.
For now, full scale production time remains the same as conventional methods.
But when we combine all the time saved in other areas, we shaved off nearly 2/3 from a typical production timescale.

To summarize, our process focuses on using AI to radically improve enzymatic efficiency and production.
For example, AI helped us stabilize our enzymes, so that they can be used many more times than conventional methods.

How much money can we save?
Based on our calculations, AI x Biotech can save 60-70% on R&D costs and 40-50% on end product costs.
Think about this for a moment: What’s more sustainable than the energy, resources, time and money that never gets used?

The gold standard of quality is, of course, natural vanillin from vanilla beans.
But it’s not mass-producible.
Its market share currently is around 1-2% of the entire vanillin market.
And it will not come anywhere close to the 76,000 tons needed by 2030.
So let’s compare the quality of mass-producible vanillins.

We compared Orchidlinn against two conventional fermentation vanillins, an eugenol-based vanillin and a synthetic vanillin, this is what we found:
Orchidlinn’s scent profile is almost identical to vanilla vanillin.
At the same concentration level, Orchidlinn’s aroma far surpasses the fermentation and eugenol vanillins in terms of aroma persistence and slow dissipation.
At 0.01% concentration, Orchidlinn achieves twice the effect compared to other vanillin products. That translates to significant cost savings to you.

I’m happy to announce that we are now production ready.
Our new factory can produce 120 metric tons of FEMA GRAS and EFSA approved ‘Natural Vanillin’.
That’s 15x times more than similar technologies!

This is no ordinary factory. We built it around our proprietary technology and processes.
We have three approved patents, with four more pending approval.
Of the three approved patents, one of them is for a method for modeling the interactions between proteins and small molecules using predefined templates or patterns.
Another is for a protein sequence alignment method, apparatus, computer device and storage medium.
The third is for an engineered enzyme variant, 4-vinylphenol decarboxylase mutant and its application, and a genetically modified microbe that utilizes this enzyme.
We’re very proud of our factory and we welcome you to come and see it in action soon.

As I mentioned earlier, there are many flavour, fragrance, nutraceutical and beauty ingredients that traditional agriculture cannot supply at scale and with consistent quality.
Besides vanillin, we’re using AI x Biotech to produce the following products:
•High cis-MDJ - a powerful, sweet-floral, and jasmine-like scent used in perfumes.
•Apigenin - a bioflavonoid with antioxidant, anti-inflammatory and potentially anti-cancer properties.
•DNJ - an alkaloid that modulates glucose absorption and has anti-obesity, anti-hyperglycemic, anti-obese, anti-viral and anti-tumor properties.
We believe that one day, all ingredients will be produced in this way: Naturally, and sustainably. With the help of AI.

To find out more about what we can do for you, drop by our booth 4.1D46, email me or schedule a meeting on our website.
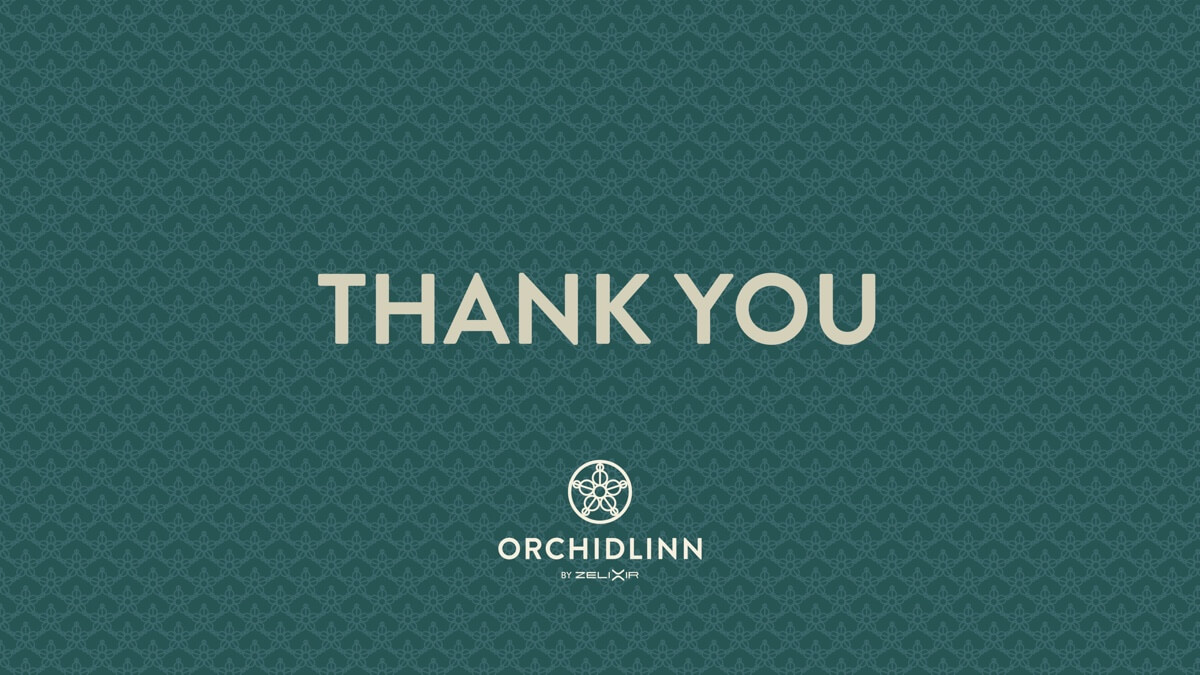
Thank you.